Each component in an ESD protected area (EPA) plays a vital part in the fight against electrostatic discharge (ESD). If just one component is not performing correctly, you could harm your ESD sensitive devices potentially costing your company a lot of money. The problem with many ESD protection products is that you can’t always see the damage – think wrist straps! By just looking at a coiled cord, you can’t confirm it’s working correctly; even without any visible damage to the insulation, the conductor on the inside could be broken. This is where periodic verification comes into play.
EPA products should be tested:
- Prior to installation to qualify product for listing in user’s ESD control plan;
- During the initial installation; and
- For periodic checks of installed products, as part of IEC 61340-5-1 Edition 2 2016 clause 5.2.3, Compliance verification plan.
“A compliance verification plan shall be established to ensure the organization’s fulfilment of the requirements of the plan. Process monitoring (measurements) shall be conducted in accordance with a compliance verification plan that identifies the technical requirements to be verified, the measurement limits and the frequency at which those verifications shall occur. The compliance verification plan shall document the test methods used for process monitoring and measurements. If the organization uses different test methods to replace those of this standard, the organization shall be able to show that the results achieved correlate with the referenced standards. Where test methods are devised for testing items not covered in this standard, these shall be adequately documented including corresponding test limits. Compliance verification records shall be established and maintained to provide evidence of conformity to the technical requirements.
“The test equipment selected shall be capable of making the measurements defined in the compliance verification plan.”
[IEC 61340-5-1:2016 clause 5.2.4 Compliance verification plan]
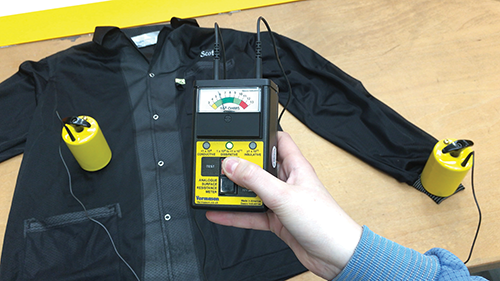
Components of a Verification Plan
As outlined in the User Guide 61340-5-2:2008, each company’s verification plan needs to include:
1. A list of items that are used in the EPA and need to be checked on a regular basis
This would include ESD working surfaces, personnel grounding devices like wrist straps or foot grounders, ionizers, etc. It is recommended to create a checklist comprising all ESD control products: this will ensure EPAs are checked consistently at every audit.
2. A schedule specifying what intervals and how each item is checked
The test frequency will depend on several things, e.g. how long the item will last, how often it is used or how important it is to the overall ESD control program.
As an example: wrist straps are chosen by most companies to ground their operators; they are the first line of defence against ESD damage. They are in constant use and are subjected to relentless bending and stretching. Therefore, they are generally checked at the beginning of each shift to ensure they are still working correctly and ESD sensitive items are protected. Ionizers on the other hand are recommended to be checked every six months: whilst they are in constant use, they are designed to be; the only actual ”interaction” with the user is turning the unit on/off. If, however, the ionizer is used in a critical clean room, the test frequency may need to be increased.
The user guide offers a solution:
“Some organizations may want to increase the time between verifications of an ESD control item after it has been in use for a period of time. This is typically done by monitoring the failures of the ESD control item. Once the organization has evidence that there is an acceptable period of time where no failures were found, the time between verifications can be increased. The new verification interval is then monitored. If an unacceptable level of failures is identified, then the verification frequency should revert back to the previous level.”
[User Guide 61340-5-2:2008 clause 4.3.3 Verification frequency]
The industry typically uses two types of verification to achieve maximum success: visual and measurement verification. As the name suggests, visual verification is used to ensure ESD working surfaces and operators are grounded, ESD flooring is in good shape or wrist straps are checked before handling ESD sensitive items. Actual measurements are taken by trained personnel using specially designed equipment to verify proper performance of an ESD control item.
3. The suitable limits for every item used to control ESD damage
IEC 61340-5-1:2016 contains recommendations of acceptable limits for every ESD control item. Following these references reduces the likelihood of 100V (HBM) sensitive devices being damaged by an ESD event. Please bear in mind that there may be situations where the limits need to be adjusted to meet the company’s requirements.
4. The test methods used to ensure each ESD product meets the set limits
Tables 1 to 3 of IEC 61340-5-1:2016 list the different test methods a company must follow. If a company uses other test methods or have developed their own test methods, the ESD control programme plan needs to include a statement explaining why referenced standards are not used. The company also needs to show their chosen test methods are suitable and reliable.
It is recommended that written procedures are created for the different test methods. It is the company’s responsibility to ensure anybody performing the tests understands the procedures and follows them accordingly.
5. The equipment used to take measurements specified in the test methods
Every company needs to acquire proper test equipment that complies with the individual test methods specified in Tables 1 to 3 of IEC 61340-5-1:2016. Personnel performing measurements need to be trained on how equipment is used.
6. A list of employees who will be performing the audits
- Part of the verification plan is the choice of internal auditors. A few suggestions for the selection process:
- Each individual is required to know the ESD Standard IEC 61340-5-1 AND the company’s individual ESD programme.
- It is essential that the selected team member recognises the role of the ESD control programme in the company’s overall quality management system.
- It is recommended that each nominated worker has been trained on performing audits.
- The designated employee should be familiar with the manufacturing process they are inspecting.
7. How to deal with non-compliance situations
Once an audit has been completed, it is important to keep everyone in the loop and report the findings to the management team. This is particularly vital if “out-of-compliance” issues were uncovered during the audit. It is the responsibility of the ESD coordinator to categorise how severe each non-conformance is; key problems should be dealt with first and management should be notified immediately of significant non-compliance matters.
Results of audits (especially non-compliance findings) are generally presented using charts. Each chart should classify:
- The total findings of the audit;
- The type of each finding; and
- The area that was audited.
It is important to note that each company should set targets for a given area and include a trend report. This data can assist in determining if employees follow the outlined ESD control programme and if improvements can be seen over time.
An example of a Verification Plan using ESD flooring for demonstration purposes is shown to the right.
A few notes:
- Our sample company has 2 different areas where ESD floor matting is used: the packaging area and the main EPA.
- Flooring is not used for grounding personnel handling ESD sensitive items.
- Our sample company has established that the limits outlined in the standard are suitable for their internal requirements.
Bear in mind that all your ESD control items need to be included in your verification plan. So, if your company uses wrist straps, smocks, chairs, gloves etc. then all of them must be listed as part of your ESD control programme.
Periodic Verification of ESD Control Products
Below you will find a list of ESD control items commonly used in an ESD protected area and how to verify their compliance with the ESD Standard:
1. Working Surface Matting
The purpose of ESD bench matting is to ensure that when charged conductors (conductive or dissipative) are placed upon the surface, a controlled discharge occurs and electrostatic charges are removed to ground. However, this only occurs if the ESD work surface is actually connected to ground. If the matting is out-of-spec, not grounded at all, the stud on the mat has become loose or the ground cord has become disconnected, charges cannot be removed.
Many companies use a daily checklist, which includes the operator having to verify that ground cords are firmly connected.
Remember to regularly clean your bench matting to maintain proper electrical. Do not use cleaners with silicone as silicone build-up will create an insulative film on the surface.
The company’s compliance verification plan should also include periodic checks of work surfaces measuring:
- Resistance Point-to-Point (Rp-p), and
- Resistance-to-ground (Rg).
Surface resistance testers and 2 x 2.5kg probes can be used to perform these tests in accordance with EN 61340-5-1 Electrostatics and its test method IEC 61340-2-3; if these measurements are within acceptable ranges, the working surface matting and its connections are good. Standard surface resistance testers will typically advise if measurements are within the range recommended by the ESD Standard (Rp-p: 106 – 108 ohms and Rg: 106 to 5 x 107 ohms per EN 61340-5-1).
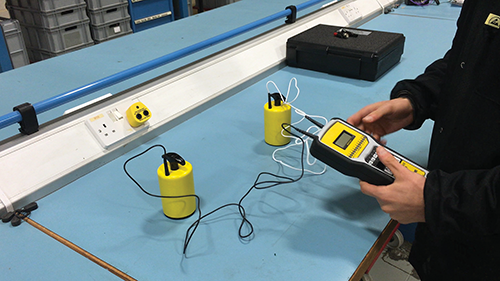
2. Wrist Straps
As discharges from people handling ESD sensitive devices cause significant ESD damage, the wrist strap is considered the first line of ESD control.
Before handling ESD sensitive items, you should visually inspect the wrist strap to see if there are any breakages etc. The wrist strap should then be tested while worn using a wrist strap tester. This ensures all three components are checked: the wrist band, the ground cord (including resistor) and the interface with the wearer’s skin. Records of each test should be kept. Wiggling the resistor strain relief portion of the coil cord during the test will help identify failures sooner. Analysis and corrective action should take place when a wrist strap tester indicates a failure.
It is recommended that wrist straps are checked at least daily. Wrist strap testers will indicate failures. An even better solution to daily wrist strap checks is the use of continuous monitors. They will alarm if the person or work surface is not properly grounded.
A note on working surface matting and wrist straps: if you are using earth bonding points, earth bonding bars etc. to ground the operator and/or bench matting, remember to inspect and test those regularly as well (every 6 months, for example).
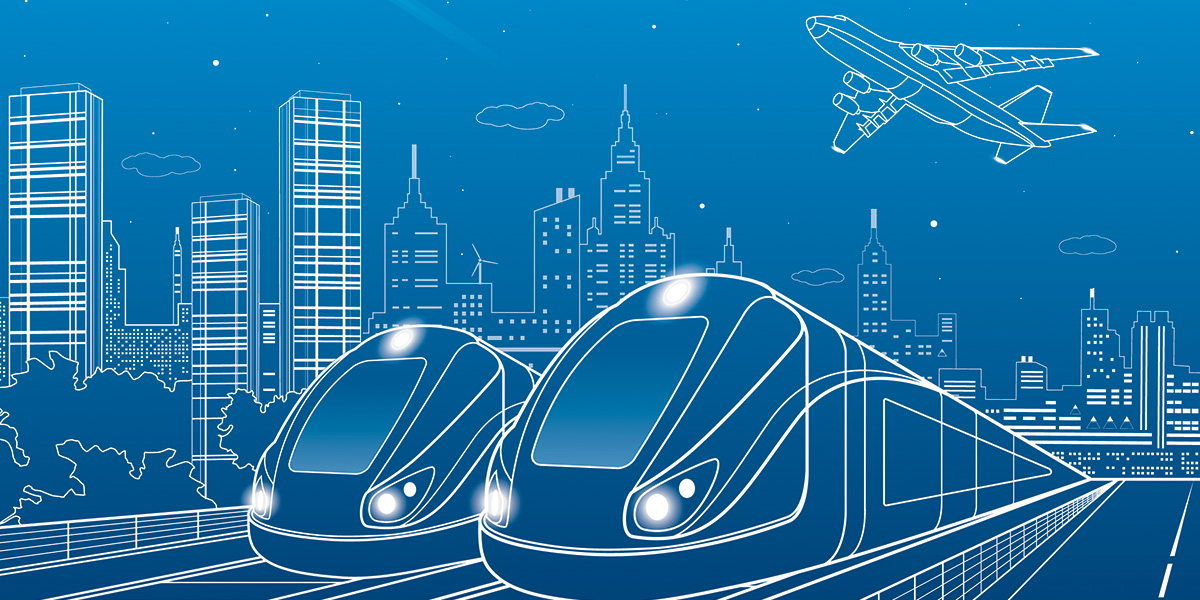
3. Floor Matting
A flooring/footwear system is an alternative for personnel grounding for standing or mobile workers. Foot grounders quickly and effectively drain the static charges which collect on personnel during normal, everyday activities. Foot grounders should be used in conjunction with floor surfaces which have a surface resistance of less than 1010 ohms.
As ESD floors get dirty, their resistance increases. For optimum electrical performance, floor matting must be cleaned regularly using an ESD mat cleaner. Do not use cleaners with silicone as silicone build-up will create an insulative film on the surface.
Dissipative floor finish can be used to reduce floor resistance. Periodic verification will identify how often the floor finish needs to be applied. As the layer(s) of dissipative floor finish wear, the resistance measurements will increase. So, after some amount of data collection, a cost-effective maintenance schedule can be established.
Floor matting can be checked using a resistance meter and 2 x 2.5kg probes. Surface resistance meters are designed to measure resistance point-to-point (Rp-p) or surface to ground (Rg) in accordance with EN 61340-5-1 Electrostatics and its test method IEC 61340-4-1. The ESD Standard recommends a resistance range of < 1 x 106 ohms for Rp-p which will remain low enough to act as a path to ground with normal dirt and grime build up on a floor and meet the required limit of EN 61340-5-1 (< 3,5 x 107 ohms) for a person/footwear/flooring system.
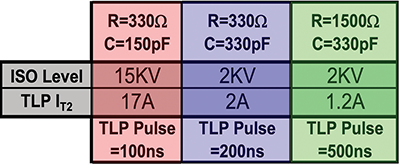
4. Footwear
ESD shoes or foot grounders play an essential part in the flooring/footwear system.
Before handling ESD sensitive devices, visually inspect your ESD footwear for any damage. Just like wrist straps, footwear should be checked while being worn using a wrist strap/footwear tester.
Records of each test should be kept. Analysis and corrective action should take place when a footwear tester indicates a failure. Footwear needs to be checked daily.
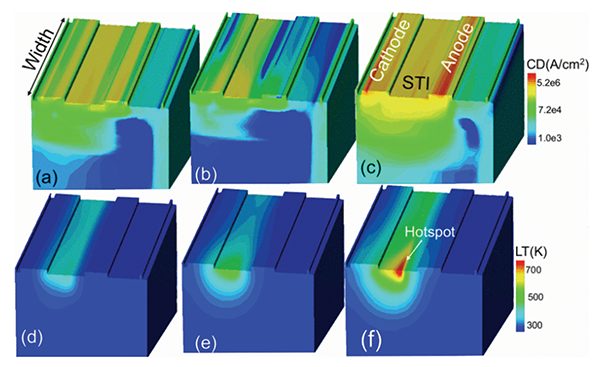
5. ESD Packaging
Re-using shielding bags is acceptable if there is no damage to the shielding layer. Shielding bags with holes, tears or excessive wrinkles should be discarded.
It is up to the user to determine if a shielding bag is suitable for re-use or not. The testing of every bag before re-use is not practical. Many companies will discard the shielding bag once used and replace it with a new one. Others will use a system of labels to identify when the bag has gone through five handling cycles, as follows:
- Non-reusable labels are used that require the label be broken to open the bag;
- The bag is then resealed with a new label; and
- When there are five broken labels, the bag is discarded.
The same principle applies to other ESD packaging, e.g. component shippers.
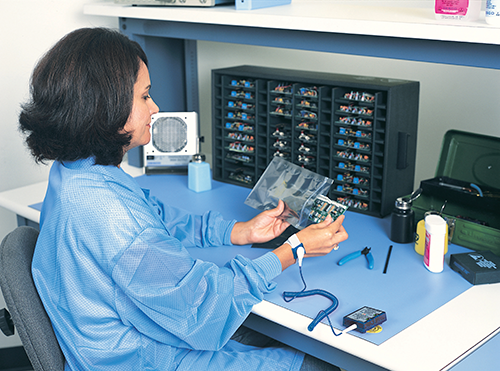
6. Ionizers
Ionizers are intended to neutralise static charges on insulators thereby reducing their potential to cause ESD damage. However, poorly maintained ionizers with dirty emitter pins and out-of-balance ionizers can put a charge on ungrounded items.
Remember to clean ionizer emitter pins and filters regularly. You can now even purchase ionizers that will alarm when emitter pins need to be cleaned or the ionizer is out of balance.
Using an ionization test kit, it is recommended to measure the offset voltage (balance) and charge decay time of ionizers. A quarterly check is sufficient.
The ESD Standard requires the offset voltage of ionizers to be ± 50V. A discharge time of <6s to get from 1,000V to 100V is typically advised. Grounding the ionization test kit, it should be placed in the airflow of the ionizer. This method measure the balance (offset voltage). Next, place a 1,000V charge on the isolated plate of the test kit and place it on a working surface. Measure the time it takes for the charge to be reduced to 100V.
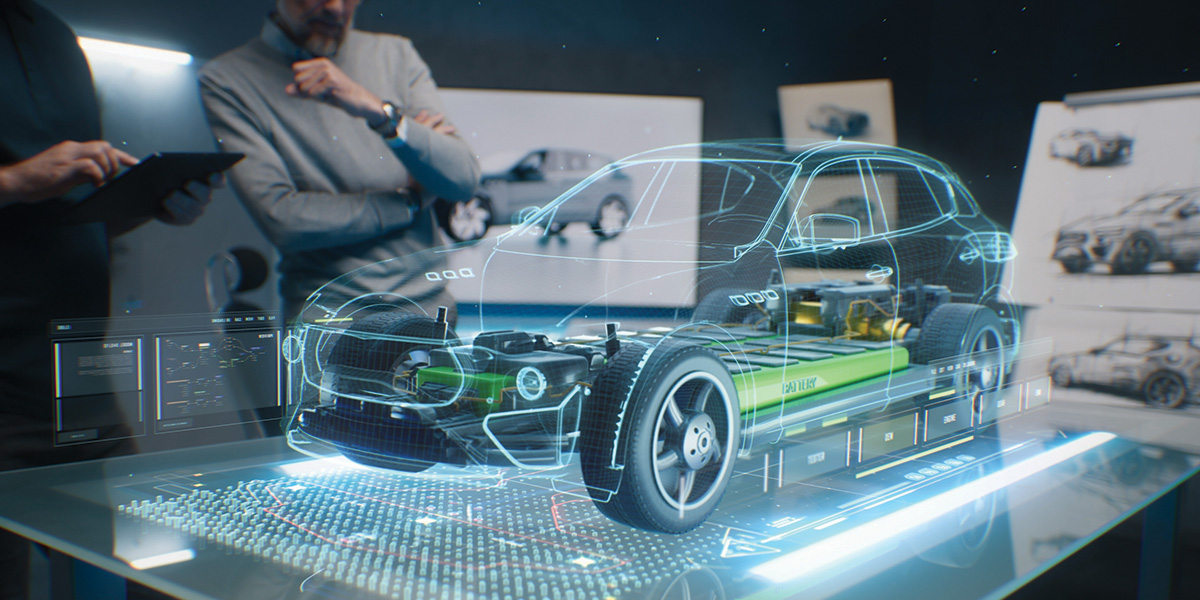
7. Wrist Strap/Footwear and Resistance Testers etc.
So, you check your wrist straps and/or footwear and bench and/or floor matting regularly. But have you remembered the testers themselves? What good do all the checks do if the testers you use are out-of-spec and show you incorrect results?
Yearly calibration is recommended – many manufacturers offer a calibration service or alternatively you can purchase calibration units from them and perform the calibration yourself.
There you have it – a list of the most commonly used products in your ESD protected area that you should check on a regular basis.
Kathleen Ranneck is the Marketing Manager for Desco Europe, the leading manufacturer of ESD Control products in the UK. Kathleen has a degree in Business Engineering and over 13 years of experience in the ESD industry. She is responsible for developing and driving Marketing and Social Media strategies. B2B Marketing is notorious for meaningless words and manufactured problems. Kathleen’s approach is to simplify the subject without condescension – whether she’s writing a blog or designing a flyer, there is a genuine concern for accuracy. Kathleen can be reached at Kathleen.Ranneck@Desco.com.