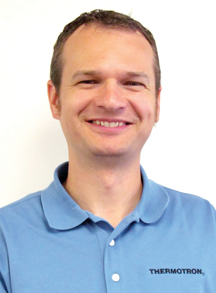
Conducting a Thorough Due Diligence Can Help You Save Money and Avoid Disappointment
Buying a used test chamber can save time and money in the short term. However, without proper insight and research, you might soon encounter many more issues that could quickly negate any initial savings. We recommend compiling as much information as possible about the used chamber in order to make an informed decision about a capital equipment purchase. In order to help, here’s a list of 10 questions you should ask the chamber reseller to help you determine if purchasing a used environmental test chamber is the best option for your company.
Question #1: How old is the test chamber?
Start out with an easy question that the reseller should have an answer for: When was the chamber built? Does the seller actually know or is it just a guess? While it is true that a well-built chamber can last decades, the reality is that, no matter how well a test chamber is built, the amount of time it properly functions depends on how hard and frequently the test chamber has been used, and its maintenance, service, and calibration history. This leads us to our next two questions.
Question #2: Was the chamber properly cared for?
Service, calibration, and maintenance records are extremely important to the history of a used chamber. What work was done? When was it done? Do you have records for it? Ask the reseller all these questions and ask follow-up questions. Accurate service records will help determine the chamber’s condition and can be used to predict its reliability in the future. If a used chamber has had yearly calibration and preventive maintenance service, there is a greater likelihood that it will meet your requirements and expectations in actual use.
Question #3: How was the test chamber used?
Certain types of environmental testing can be more strenuous on a chamber than others. Sometimes test chambers are run to the extremes, constantly ramping up and down in temperature, and operating continuously over several days or even weeks. It’s helpful to know how the chamber was used and in what type of environment the chamber was operated. Was it in a clean lab environment or was it in a dirty and dusty manufacturing plant?
Another possible issue with a used chamber is the types of products that were previously tested in the chamber and whether they may have leached chemicals during testing. If so, the chamber’s integrity and performance may be compromised. In addition, if the used test chamber has a humidity feature, what kind of water was used? If the water used did not meet minimum purity standards, the internal tubing could be corroded or ruined.
Question #4: What type of refrigerant is used in the chamber’s cooling system?
In 1995 the U.S. federal government passed regulations prohibiting the use of certain types of refrigerants, which are used to cool environmental test chambers. (The Montreal Protocol banned chlorofluorocarbons—CFCs—which includes many older types of refrigerants.) If an environmental test chamber was built before 1995, it’s possible that the chamber is cooled with refrigerants that are no longer permitted. Further, it may be difficult to fix refrigeration leaks since replacement refrigerant may not be commercially available. The only option for repairing such a system would then be to retrofit the test chamber’s cooling system. This can be an expensive undertaking, one that could ultimately negate any cost savings you might have had when you initially purchased the used chamber.
Question #5: What type of controller operates the chamber?
It’s important to find out what controller is included with a used chamber. Is it a generic controller that only displays certain features? Or is it a controller from the original manufacturer, which allows a full range of capabilities? The controller is the “brains” of the test chamber. With the right controller you can harness the test chamber to perform at optimal levels. Frequently, the controller on used test chambers is replaced by the third-party reseller with a generic controller. When this occurs, the chamber can lose much of its promised functionality.
Question #6: What are the chamber’s utility requirements?
It is important to know the used chamber’s utility requirements to ensure its compatibility with the utilities available at your facility. Make sure you know the chamber’s electrical and voltage requirements. Is it air-cooled or water-cooled? Does it require compressed air or liquid nitrogen or CO2 supply? If your facility is not set up for what the chamber requires, it could be costly to upgrade utilities in order to accommodate the requirements of the used chamber.
Question #7: What are the chamber’s model and serial numbers?
The manufacturer’s serial number can be the key to obtaining answers about the history and health of a used test chamber. Test chamber manufacturers often retain records related to the date of manufacture, as well as information about routine maintenance and other services that may have been performed. Having the chamber’s serial number may enable you to contact the chamber’s manufacturer and verify some or all of the reseller’s claims.
Question #8: How did the reseller obtain the chamber?
Is the seller the original owner? If not, how did the reseller acquire the used chamber? They could have purchased it from the original owner or maybe they found it on Craigslist or just bought it at an auction. Knowing who has owned the equipment is important because it provides detailed information about the history of the chamber, including its operating environment and service and repair records.
Question #9: Did the reseller refurbish the chamber?
If the reseller refurbished the chamber or performed any repair work to put the chamber into a sellable condition, find out if a qualified, certified service engineer with experience in refurbishing test equipment performed the upgrade. Each chamber manufacturer is different, so upgrades can be complicated. Buying a used chamber that has not been properly refurbished can cause a lot of problems (equipment downtime and money).
Question #10: Is support available for the used chamber?
Does a product manual come with the purchase? If there isn’t a manual, do you know how to run the chamber? What if you require troubleshooting to solve some problems? What do you do when the controller doesn’t do what you want it to do? Often, when buying a chamber from a third party reseller, you’re only buying a test chamber and not getting the training and support needed to run the chamber efficiently.
What Else Do I Need to Ask?
In addition to these 10 questions, there is also a short list of questions you need to ask yourself, and those relate to the kind of chamber you need to test your products. Knowing what size chamber you need for the products you’ll be testing ensures that you’ll make the right investment. You want to make sure you find a solution that best fits your needs. Be sure to consider some of the following questions:
- Is the chamber workspace big enough for your product?
- Does it have a wide enough temperature range for all of the test specification that you need to meet?
- Will you need the chamber to have humidity capabilities?
Buying a test chamber is a big decision, and buying one from a reseller requires additional due diligence. We hope that these questions will help you to get the answers you need so that you can make an informed buying decision.