This article focuses on methodology, techniques and tools to identify, classify and quantify ESD occurrences in back-end semiconductor and electronics assembly manufacturing. Proper methodology of detecting and measuring ESD Events in working tools handling ESD-sensitive components, identifying CDM-type of discharges and associating discharges with the specific steps of the process is described in details on a level usable to a wide range of specialists. Use of tools, such as high-speed storage oscilloscopes, special antennae, ESD detectors and monitors will be explained in detail. This article should benefit increasing numbers of process engineers who are struggling to maintain yield while the devices are getting increasingly more and more ESD-sensitive.
If you are an engineer responsible for the manufacturing of semiconductor devices or for PCB assembly, and you were told that one of the ICs in your process has a damage threshold level of 100V CDM (charged device model), how would you ensure that your process is safe for such devices? If you are a user of these devices, wouldn’t you be interested to what level of ESD the ICs you just received were exposed before you got them? If the damage level is indeed 100V CDM, how would you like to work with the device that was exposed to 99V? Would 98V do?
ESD exposure to sensitive electronics components is now one of the major factors in yield and quality management. No one wants to deal with the finished product that failed at the customer because one component was damaged by ESD. And no one wants to deal with yield issues that can put significant strain on schedule in addition to the losses.
No effective ESD management can exist without means to verify the actual ESD exposure. Most “traditional” ESD prevention methods are based on assumption – the thinking goes that if one implements static-dissipative materials, ionizers, grounding and wriststraps everything will be OK. This, of course, worked well when components’ sensitivity was 500V or so and is no longer sufficient. Let’s examine the methodology and the instruments that would help us to identify and to quantify ESD exposure to sensitive devices in the manufacturing process.
Basics of Methodologies to Assess ESD Exposure to the Devices
There are several ways the ESD exposure to the devices in process can be assessed. Not all methods and tools are adequate for the purpose, though. We will examine several of the most popular methods and summarize their benefits and drawbacks.
It should be obvious to a reader that any degree of separation from the ultimate parameter of interest significantly reduces relevance and believability of data, at some point rendering them meaningless. It is a discharge after all, that damages the device, not the voltage and not the charge on the device, and most definitely neither resistivity nor ionizer balance. Therefore, measurement of anything but the discharge itself is a measurement at least once removed. Figure 1 shows how different the measurements typically done to comply with either ANSI/ESDA S.20.20 or EN61340-5-1 standards differ from the very parameter that damages the device. These standards are very helpful in establishing an environment that minimizes ESD exposure to the devices, however these standards contain no means of verification and provide no comfort to the user that the very devices they are supposed to protect are actually safe. Let’s consider methodology, benefits and deficiencies of each method.
Measurements of ESD Events
The most ideal way to measure ESD Events would be to measure the discharge current directly. These measurements are routinely performed during device characterization. Such standards as JEDEC’ JESD22-C101C and methods utilizing CDM (charged device model) and TLP (transmission-line pulse) testers perform current measurements to analyze at what voltage of discharge of certain models the device would be damaged and which specific pins are the most sensitive to ESD exposure. However accurate and desirable this methodology is, it is hardly realistic in an actual production environment simply because there is no practical way to insert a current sensor between the device and the surface it touches, such as a test socket, shuttle in the IC handler or a PCB pad. Only when the test is done under specially-controlled circumstances using customized fixtures are such measurements possible. The biggest problem with them is that they may bear very little relevance to real-life discharges in the process, thus defeating the entire purpose of increasing accuracy of measurements. The most practical way of detecting and measuring ESD Events in the actual manufacturing process is by capturing a very specific electromagnetic signature generated by an ESD Event –
this way the process itself remains uninterrupted and unaffected by measurements. An ESD Event is characterized by two simultaneous phenomena – sudden drop of voltage in part due to its discharge and a very short current surge of discharge itself. Both phenomena create electric and magnetic fields accordingly. By capturing and measuring these fields it is possible to assess the strength of the discharge and by observing its waveform, the type of discharge (CDM, MM or HBM).
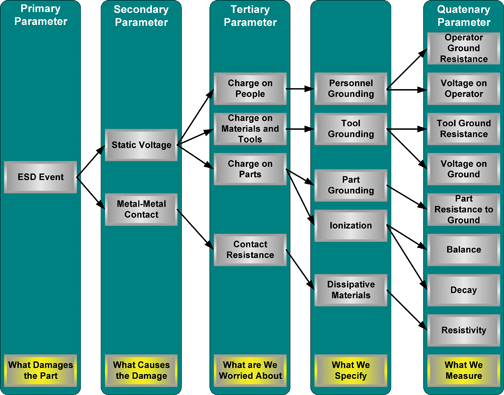
Measurements of electromagnetic fields are not exactly as accurate as direct current measurements due to reflections of the electromagnetic waves and attenuation due to metal barriers; however, properly performed they can offer reasonable accuracy and relevance.
Figure 2 shows the correlation between direct current measurements in a specially-designed test fixture and the electromagnetic signal generated by the discharge and captured by an antenna located nearby. As seen, both traces track reasonably well providing confidence in relevance and in accuracy of the obtained data.
Figure 2: Measured ESD Event Strength with current and field measurements
Correlation with the Strength of Events
The correlation of captured data with the strength of ESD Events is a daunting task. Environmental variables present significant possibility of error. Difference in device package size can offer a large variation in both discharge current and accompanying electromagnetic emission. A SOT23 or a DFN16 package will produce smaller artifacts than, say, 208 QFP package. To deal with all these variations it may be helpful to set reference to some established standard so that users can correlate their specific packages to the standardized ones. JEDEC JESD22-C101C defines two sizes for simulation: small metal disk (diameter 8.89mm, thickness 1.27mm) and large metal disk (diameter 25.4mm, thickness 1.27mm). Correlation of ESD Event artifacts such as discharge current and/or electromagnetic field signature to these models may help in establishing a reference to which all the variations of the package can correlate this way or the other.
Lack of such correlation leads to qualitative, not quantitative measurements which, by nature, are much less valuable. If your devices can be damaged by 100V CDM discharge, wouldn’t you want to know what your process actually generates? A waveform on the screen of an oscilloscope or a “beep” of an indicator while providing some information may not be able to answer this question while reading of the instrument capable of correlation with actual ESD Events would be of significant value.
Time Domain vs. Frequency Domain
Electrostatic discharge or ESD Events last a few nanoseconds. As such, they require a certain approach in order to capture the signal and to quantify it. An ESD Event is a time-domain phenomenon. It is not periodic like a sinewave and it lasts a very short time. As such, ESD Events must be measured with time-domain instruments, not with the frequency-domain tools such as spectrum analyzers – the latter are simply too slow to capture the event. A spectrum analyzer which is an excellent tool for many other purposes, measures signals at one frequency at a time. It takes at least several milliseconds for the top-of-the line models to span the entire frequency range. Since an ESD Event lasts only few nanoseconds, the spectrum analyzer is certain to miss a significant portion of the spectrum of the signal. Only proper time-domain instruments described below are suitable for capturing and measuring
ESD Events.
One of the common questions I get about ESD Events is what their frequency range is. Since an ESD Event is a non-repeatable signal, it cannot have frequency. However, it does have a spectrum which for most of ESD Events extends from low Megahertz to a Gigahertz or higher. Some digital storage oscilloscopes have built-in FFT module which allows observing the spectrum of the captured signal. With all this in mind, information on spectrum of an ESD Event is rather academic. What really affects the damage to the devices are time-domain parameters such as event rise time, its maximum amplitude and its energy.
High-Speed Digital Storage Oscilloscope
A properly-specified and set up oscilloscope is arguably the best tool to observe the discharge waveform and to analyze the type of discharge. It is a time-domain instrument well-suited for such measurements. The choice of the oscilloscope must be done carefully – an underperforming instrument will distort the data and may lead you to wrong conclusions. There are two main parameters to consider – sampling rate and bandwidth.
Sampling Rate
Sampling rate determines how many times per second the input signal gets sampled. This parameter needs to be correlated to the properties of the signal. The rise time of a CDM (Charged Device Model) event can be well under 1 nanosecond. In order to properly represent it, at the very minimum the sampling rate must be at least twice as fast according to Nyquist-Shannon sampling theorem. The higher the sampling rate the more accurate the representation of the waveform will be. It is quite possible to obtain on the market today at a reasonable price an oscilloscope with 5Gs/Sec (Gigasamples per second) which is recommended minimum sampling rate.
Bandwidth
This parameter, though important, is actually less critical than the sampling rate. Insufficient sampling rate will result in significantly distorted waveform or missing signal artifacts, while limited bandwidth usually results in lower amplitude of sharp peaks but still showing their waveform.
Overall, the minimum specification for an oscilloscope is recommended to be 5Gs/Sec sampling rate and 500MHz bandwidth, though the higher both parameters are, the better quality representation of the signal the user gets.
Antenna
Electromagnetic fields are measured using specialized antennae. A selection of antenna may prove to be critical. A typical antenna or a probe for electromagnetic compliance (EMC) is not advisable – such antennae do not have flat response across the frequency band. When used with the spectrum analyzer, this analyzer provides amplitude correction for each individual frequency as the instrument progresses with its scan across the frequency band. In time-domain measurements all frequencies are measured at once making frequency correction for antenna imperfections impossible. Only antennae with the reasonably-flat frequency response can produce adequate representation of the waveform of the discharge. A typical EMC antenna or probe would typically have significant drop of sensitivity at low frequencies which grossly misrepresents the energy of the discharge on the screen. Figure 3 shows the comparison of frequency responses between a specially-designed time-domain active antenna with flat frequency response across the frequency range and typical frequency-domain probes. As seen, passive probes exhibit loss of over 20dB (10 times) at frequencies below 400MHz. This is analogous to turning bass completely down in your stereo and listening only to high-frequency “squeaks” instead of a complete signal. Figure 4 shows the waveforms of the resulting ESD Event captured with both antennae. Active antenna waveform is the top trace, the passive antenna response is the bottom trace. As seen, the bottom trace shows not only a much weaker event (which is explained by the fact that the signal from the passive antenna is not amplified) but also that the waveform distinctly lacks a low-frequency component which represents the energy of the discharge. The small time difference between the waveforms and the inverted polarity are the results of group delay and type of an amplifier in the active antenna.
Figure 3: Frequency responses of time-domain active antenna and typical passive probes
Figure 4: Waveforms of the same discharge captured with time-domain active antenna and a typical passive probe
ESD Event Monitors
While oscilloscopes have certain indisputable advantages for displaying signal waveforms, they do have limitations. To begin with, they can be expensive. Some oscilloscopes are complex to operate which may lead to wrong or missing data. Oscilloscopes can measure ESD Events only in limited number of points at a time which makes diagnostics of ESD problem in such complex tools as IC handlers rather difficult. Oscilloscopes can trigger only on one polarity of the signal while ESD Events can be of any polarity – obviously, some events can be missed. Oscilloscopes won’t be able to resolve multiple discharges due to triggering issues – this seriously hampers analysis of ESD problems in the process.
Dedicated ESD monitors address most, if not all, of the above issues. An example of such a monitor is shown in Figure 5. This ESD monitor is capable of monitoring not only ESD Events but also static voltage which helps with ESD diagnostics. An ESD monitor detects ESD Events and measures their strength. Unlike an oscilloscope, an ESD Event monitor cannot produce a waveform of the discharge. Instead, it measures the properties of the waveform of the discharge and generates a signal that is a reflection of the discharge’s strength. Figure 6 shows an example of the data from an ESD monitor.
Figure 5: ESD Monitor
Figure 6: Typical data from ESD monitor including static voltage and ionization decay
This particular ESD monitor is fully characterized for different models of discharge so that the user can know that a particular event was, say, 100V CDM, or 200 V CDM. Another key feature of this monitor is its ability to resolve multiple discharges which becomes critical in fast-moving tools. These monitors are connected to a data acquisition system which can accommodate a substantial number of such monitors enabling ESD diagnostics and troubleshooting in several locations simultaneously.
ESD monitors are easy to use, and together with data acquisition system they keep records of everything they see in the process. ESD monitors can be used for a variety of purposes:
- ESD problem diagnostics
- ESD audits
- ESD Qualification of the tools and the processes
- Supplier audits
- And many others.
ESD Event Meters
While ESD Event monitors require setup and connection to a computer to record and to display the data, hand-held ESD Event meters such as one pictured in Figure 7 allow collection of data on ESD Events without any special setup. Such instruments are capable of detecting, measuring and characterizing ESD Events and recording them on a memory card with time/date stamp. Though such instruments can measure ESD Events only at one spot at a time, it allows for a very convenient, fast and accurate way of diagnosing an ESD environment. The instrument allows use of a remote antenna similar to the ESD monitor pictured in Figure 5 to capture discharges inside the tool where the meter itself won’t fit or would be inconvenient or unsafe to hold it inside the process.
Figure 7: ESD Event Meter
ESD Event Indicators
ESD Event Indicators, such as the one shown in Figure 8, count ESD Events above a set threshold and show their relative strength on an LED bar. The readings and the thresholds are relative, but the instrument is fairly inexpensive and is extremely easy to use. It also offers separation of CDM-type ESD Events from other types of electromagnetic emission.
Figure 8: ESD Event Indicator
What About Static Fieldmeter?
A ubiquitous hand-held fieldmeter is widely used in production environment for measurements of accumulated static voltage. However convenient such instruments are for measurement of voltage on the semiconductor devices, they have limitations – any instrument does. Once we know what the limitations are, we would be in a better position to use the instrument for the purpose intended and to understand its reading better. Below are just a few limitations of this device.
Large vs. Small Device
Static voltmeters are typically calibrated at 1” from an infinitely large uniformly charged surface. A small semiconductor device is anything but infinitely large. Viewing angle of a typical fieldmeter is quite large and the meter integrates everything it sees in its view. As a result, a SOT or a DFN package charged to 100V may read only 15V on the meter. A temptation to bring the instrument closer to the device only further skews the results since the distance won’t be 1” anymore and the readings will be seriously affected without any means to know to which degree.
Detection Speed
Static fieldmeters have inherent detection speed limitations. First, is its display limitations. A typical refresh rate of the display is three times per second to accommodate for human eye abilities. Fast-moving devices may pass by without the meter ever registering the voltage. Even when a fieldmeter is connected to a recording device via its analog output, the vibrating sensor inside a fieldmeter (you can hear it work by bringing it close to your ear) would still limit reaction time. At best, the voltage readings would be artificially low, at worst, the voltage may go unnoticed.
There are specialty static voltmeters available that can improve the situation, however still they are no match for genuine ESD Event measurements.
Conclusion
Among many types of measurements performed for ESD assurance, only one measurement truly relates to the ESD exposure to the device – measurements of ESD Events themselves. These measurements provide factual information highly relevant to those who’s job is to assure that no devices in production process are being exposed to unacceptable levels of ESD as well to those who will be using these devices to assemble PC boards and finished products. Only results-based ESD management can be truly effective and this is what ESD Events measurements provide.
Vladimir Kraz, a principal in BestESD Technical Services, has over 30 years of experience in the electronic industry. He designed some of the best-in-class ESD and EMI instruments. Vladimir has 21 U.S. patents with more patents pending. Vladimir wrote numerous articles for technical publications, presented papers at ESD Symposiums both in the U.S. and abroad and taught classes and conducted seminars on the subject of ESD, EMI and EMC around the world. Vladimir is a member of several technical associations, including ESD Association and IEEE. He can be reached at vkraz@bestesd.com.